Corrugated Transformer Tank
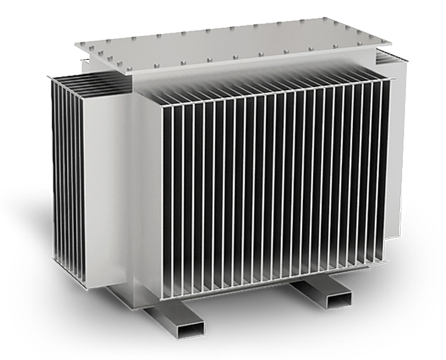
KEY FEATURES OF CORRUGATED TRANSFORMER TANK
Strong construction & smaller footprint
- No blockage of oil flow into the fins
- High efficiency cooling
- Improved heat dissipation
- Oil cleaning is easier & economic
- Less oil & less steel required
>30% Potential for saving in material
>30% Reduction in the weight of the transformer
>30% Reduction in the overall volumetric dimension Range - Manufacturing capacity of corrugated wall panels / Fin walls for transformer tanks and complete corrugated transformer tanks up to 10 MVA.
The role of fin walls is to increase the surface area in contact with cooling air. Due to the temperature rise of the winding under load, the oil temperature also rises. The hot oil rises upward to the top cover and goes down into the fins where it is cooled by the air rising up between the fins. Hence the heat dissipation becomes faster.
Thus, MS corrugated wall panels / fin walls have eliminated the use of radiators which were a part of traditional transformers tanks, as the fin walls acts as an excellent Hent Exchanger. Following are the key features of corrugated transformer tanks:
The corrugated fins are manufactures using a special cold rolled MS coil and are directly welded to form the transformer tanks.
These fins have sufficient degree of elasticity to absorb expansion in volume of the liquid (insulation oil) and it also provides a large surface area to dissipate the heat generated.
Transformers with corrugated walls are compact compared to transformers with radiators, thus reducuting the space for installation.
The corrugated fin walls with vertical embossed channels provide greater stability to the corrugated fin walls.
The numbers of welded joints are reduced, thereby, reducing the chances of leakages and also production time.
The Transportation cost it lower due to reduction in weight and overall dimensions.
It enhances aesthetic appeal compared to the traditional transformer tank.
Laser Cutting and CNC Bending
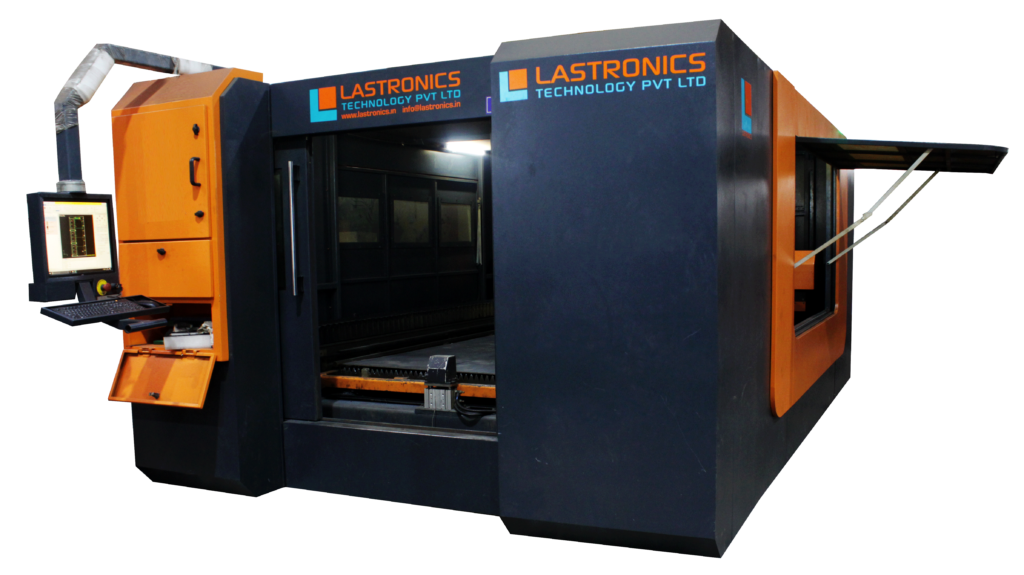
Laser cutting is a thermal cutting method which is used in the cutting of conductive metals. In the cutting process, the gas flowing through the torch is energized. High temperature laser gas flow which ionising by energy is directed to positive pole material from the mouth of the nozzle. The material is pushed by the jet effect of the gas and the cutting process takes place.
Advantages of Laser Cutting:
• Precise cutting process and high cutting speed
• High mechanical precision
• High axis positioning speed
• X and Y axes moving on precision linear rails
Laser cutting and bending operations are used in the production of intermediate products such as tank cover and bottom plate manufacturing.
In our factory we can cut and bend metals up to 20mm thickness.
Since it has been founded Micro-Mech Engineers has completed numerous projects successfully and now offering to you its experience, know-how and the understanding of ethical business in manufacturing transformer tanks, wave walls and radiators. Our company makes customer oriented production in its high tech facilities. In the 3000 m2 production space and with its expert technical team, Micro-Mech Engineers offers its services essentially in those areas;
1. Laser cutting & bending
2. Corrugated fin wall production (80 tons/month)
3. Transformer tank production (200 pcs 400 KVA/month)
4. Surface preparation
5. Painting
Fin Wall production
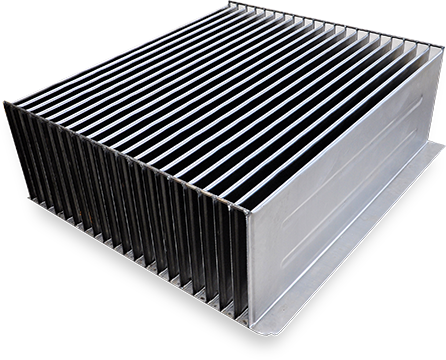
HOW TO MAKE WAVE WALLS?
DKP (CCR) 6112 A1 quality cold rolled, monolithic roll sheet, wave wall processing machine is transformed into honeycomb transformer elements are called wave wall.
The technical document containing the customer demand is worked on and the production parameters are adjusted to the specifications of our machine and entered into the system.
DKP 6112 roll sheet metal is produced by fully automatic PLC drive wave wall machine according to the parameters of customer request.
Wave walls are transferred to PLC controlled welding robot. Seam welds at the honeycomb joints are welded in a seamless and leak-free manner with synergic gas welding machines integrated into the welding robot.
Wave to wall strengthening transmission rods and belt are welded.
According to the boiler installation details, the wave walls are made ready for use by folding at the start and end points of the wave wall.
Wave walls are subjected to final inspection during the quality control process.
Notes:
- In cases where the fin height exceeds 200 mm, the grooves pressed into the center of the fin increase the strength of the wave wall core, allowing the core to expand and constrict 10,000 times.
- In our factory, short and long side wave walls can be grouped together.
- The mini grooves between the two honeycombs in our wave walls increase the strength of the wave wall.
- Our capacity is 80 tons per month
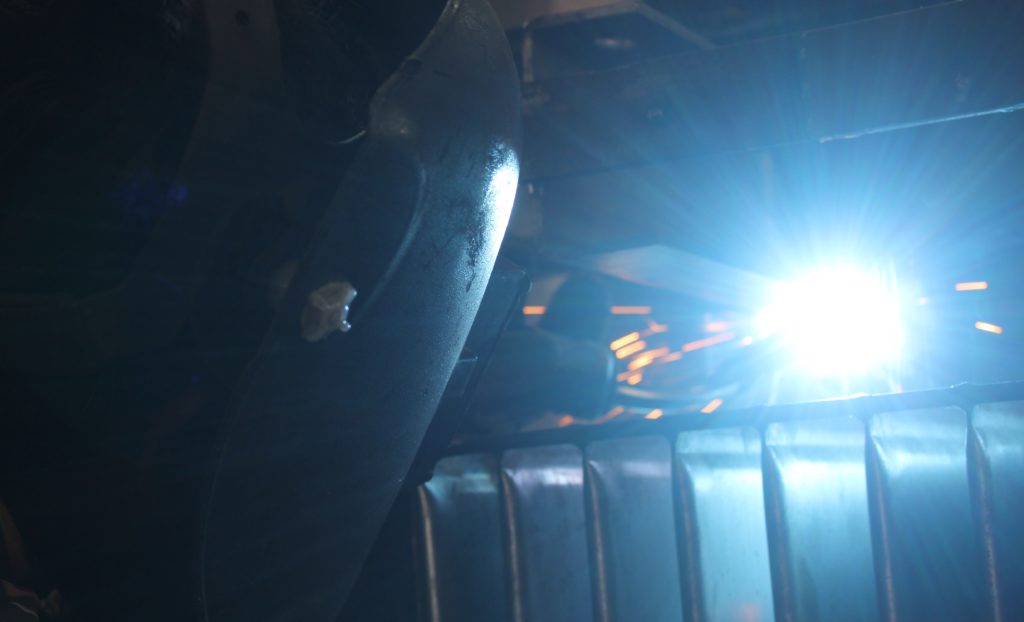
TRANSFORMER COOLING SYSTEMS
Iron and copper losses during the operation of oiled-type electric transformers cause the active part of the transformer to heat up. This heat disrupts the structure of the materials that form the active part of the transformer over time.
The distribution and power transformers need a cooling system to remove this heat.
Transformers:
- ONAN “Oil Natural Air Natural”
- ONAF “Oil Natural Air Forced”
- OFAF “Oil Forced Air Forced”
- OFWF “Oil Forced Water Forced”
- ODAF “Oil Directed Air Forced”
- ODWF “Oil Directed Water Forced” can be produced with 6 different cooling systems.
Transformer tanks according cooler types:
- Tanks without cooler
- Corrugated wall type tanks
- Radiator panel type tanks
- Tubuler cooling type tanks
Cover Conservator and cable box
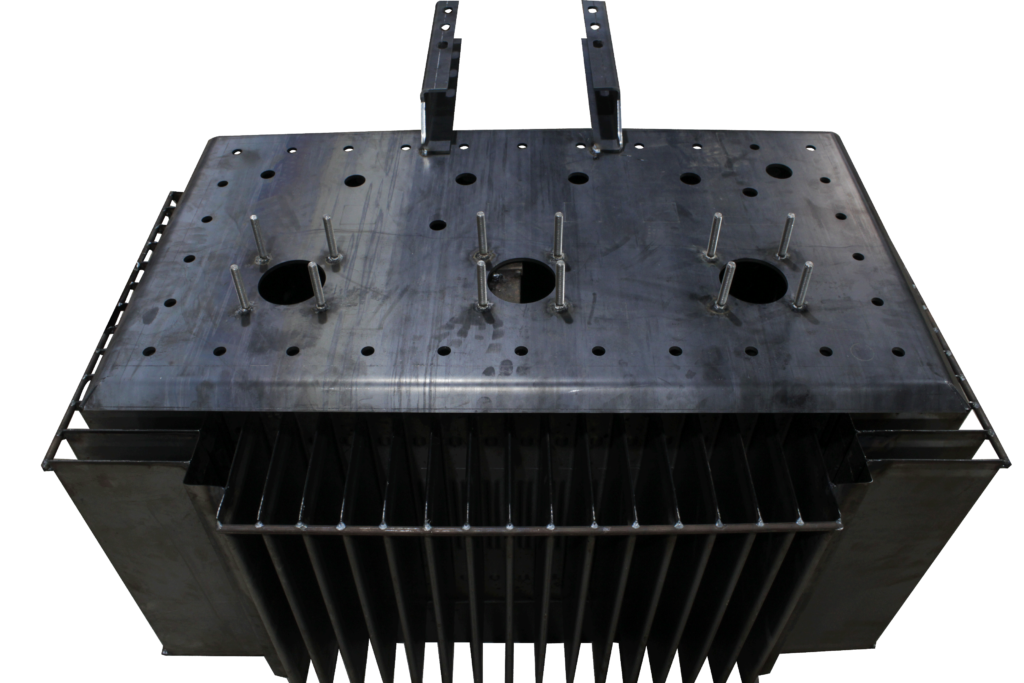
TRANSFORMER BOILER COVER
It is the top plate of the boiler cover inlet and outlet bushings and the oil meter, thermometer and tap changer. Boiler cover, bushing studs, lifting ears, thermometer pocket, oil filling sleeve, active part lifting device, anti-magnetic ag bushing plate (if any) and expansion tank connection elements, etc. It is completed. Points to be considered in the manufacture of covers.
- Retention of dimensions and dimensions,
- Proper and smooth cuts of hole diameters and position
- No leakage in resources,
- No welding burr is formed on the surface.
WHAT IS GENERALIZATION STORE (RESERVED)?
Electrical distribution and power transformers are manufactured in hermetic or expansion tank type. The increase in heat caused by the losses of I2R and hysterisis in transformer boilers with generalization tank causes the insulation oil to expand and increase its volume. Expansion tank (reserve) is used to find the empty volume of the expanded insulating oil without deforming the transformer boiler.
This cylindrical tank, which is mounted on the lid of the boiler, creates an empty space to fill the expanded oil. With the oil filling cap on it, the added oil can be added.
In addition, the moisture retainer and the moisture coming to the surface of the expansion tank are kept in the slicagel, thereby extending the life of the transformer. Again, the horizontal oil indicator on the side surface of the expansion tank is used to monitor the transformer oil level.
According to customer demand, Bucholz Rolesi is installed between transformer boiler and expansion tank.
Surface Preparation and Painting
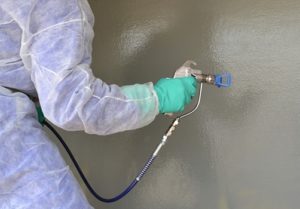
SURFACE PREPARATION
The performance and durability of all paint coatings are significantly influenced by the surface preparation. In the case of steel structures, this becomes more important. The choice of surface preparation method is crucial to the prevention of corrosion. The practical performance of paint coatings is significantly influenced by the condition of the surface before painting. Basic related factors:
- Rust and iron oxide layer
- Presence of contaminants such as salt, dust, oil and gress
- Surface profile
ISO 8501 provides a visual assessment method for cleaning surfaces and is widely used to identify surface coating systems. This standard is divided into 4 sections as Sa1, Sa2, Sa 2½ and Sa 3.
Before painting and coating, the steel surface must be cleaned of all oil, rust and paint residues. In transformer boilers, sandblasting is the most effective way to obtain a smooth and clean surface. During blasting, grit is applied to the surface by means of compressed air. Thus, the surface is cleaned by abrading at the desired rate. Grit size varies according to the abrasion rate and since thin metal plates are used in transformer boilers, silica sand with extra thin types is used.
The transformer boilers are sandblasted in the sandblasting cabinets of Micro-Mech Engineers In addition, our company has the necessary drying, ventilation and filtration systems for sandblasting cabinets.
PAINTING
As is known, power and distribution transformers are the most expensive components of power transmission lines. Transformers can operate efficiently during the planned time, especially with cooling system components and good maintenance. We choose the best painting method and material according to customer requirements and the possibilities of our painting plant and produce 100% coated anti-corrosion surfaces.
The drainage technique is the most common method used in transformer tanks. With this method, wave walls, thermometer pockets, bushing connection points and lifting ears can be painted in an open area. In addition, the wave wall interior of the tank is completely painted and surface protection is provided in the best way.
We offer you surface preparation and painting processes together. Transformer boilers, which are painted by pouring paint technique after blasting process, have more surface strength and longer life than boilers painted according to traditional techniques.